First Cerruti Pelican R982 press ready to ship to customer

Rajkot, which is a v-hour bulldoze westward of Ahmedabad, has go a food processing and packaging centre likewise as an important cluster for the manufacture of world-course packaging equipment for the flexible packaging manufacture. From blown motion picture lines up to vii-layers, to co-extrusion equipment and gravure presses, the local industrialists are building elegant new factories and acquiring the latest technologies from global leaders. The aim is not just to supply to the booming Indian flexible packaging industry but to export to wider markets by making high spec equipment with the support of leading and well-accepted global brands.
In Rajkot y'all hear the expression 'down to earth' quite often – to describe the meteoric ascension of several successful industrialists who remain hands-on in running their family-owned enterprises. They are risk takers who invest serious money in the best infrastructure, manufacturing equipment, software tools and human resources. In the instance of several industrialists, including Pelican'due south possessor Bharat Shah, this has also meant acquiring and integrating best in class technologies that are appropriate and competitive either through joint-venture or technology licensing with branded marketing rights.
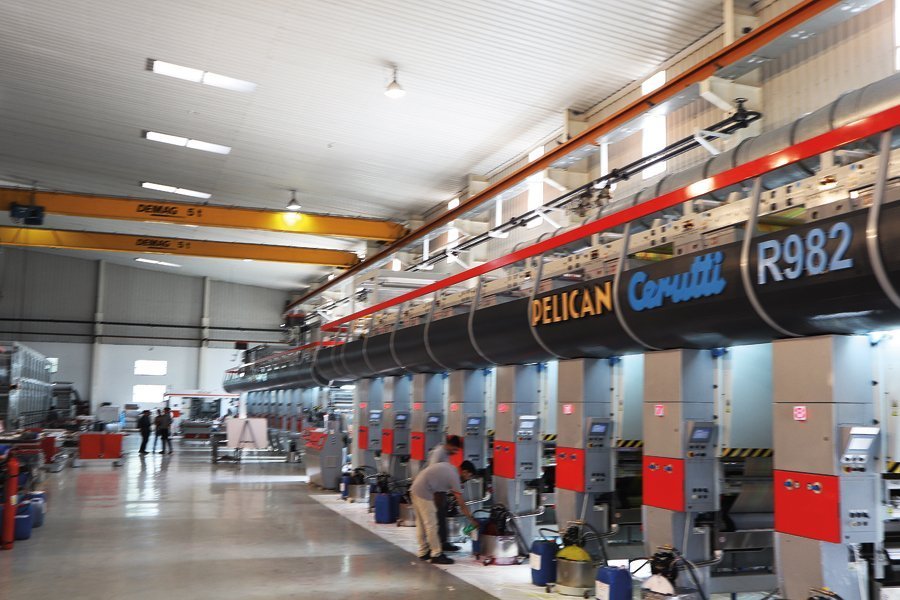
Pelican was already acknowledged every bit the leading gravure press manufacturer in Bharat among 3 who are known to be excellent global suppliers. Fifty-fifty before its licensed manufacture of the Cerutti R982, its Solomark presses with mechanical line shaft and servo technology were chosen by leading Indian converters that export packaging materials to supplant gravure presses from the leading European manufacturers.
When the get-go Cerutti Pelican R982 9-color press was shown at the PlastIndia exhibition in Gandhinagar in February 2018, I asked one of the other ii leading manufacturers as to who led the number one spot. Without hesitation he said, "With the mechanically running demonstration of the first press based on the Cerutti collaboration, it has to exist Pelican."
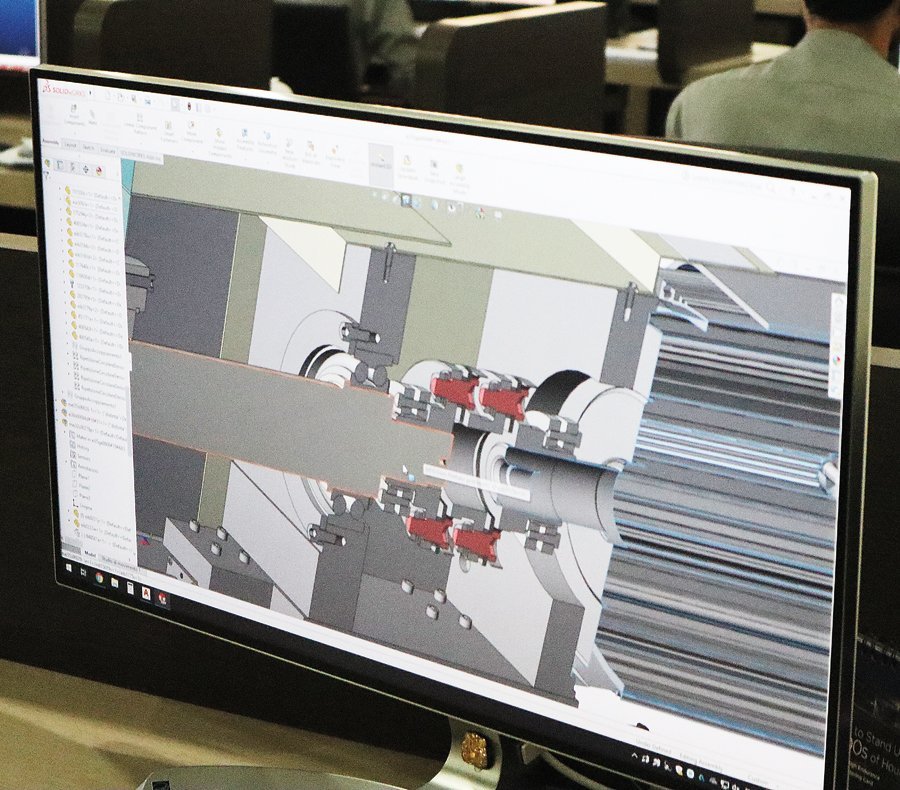
The R982 gravure press with both shaftless chucking or shafted cylinder mounting brings Pelican into the 450 meters a minute category as Indian converters gear upward for higher volumes and efficiencies. With a maximum width of 1.3 meters offered, the press is capable of web tensions from 60 to 400 Northward. "This is an especially important spec based on a dancing roller mounted on a pivoting lever with a counterweight, which along with the other precision features of the press enables converters and brand owners who are increasingly looking at using thinner, more than extensible and easier to recycle laminates," says Shah, calculation "sustainability is the driving issue for the Indian flexible packaging industry going forward."
All Pelican equipment is based on Siemens electronics that are systematically mounted for ease of installation and servicing in standardized cabinets. The electronic line shaft, integrated register command from Baldwin Vision Systems, well-designed cylinder carts which slide on a linear guide rail and most of all, loftier efficiency drying and ventilation modules congenital for sustainable reuse of energy and solvent extraction are some of the modern features of the new gravure press that enable information technology to sustainably achieve loftier quality at 450 meters a infinitesimal. In addition to the upper heat ventilation organisation, there is a divide fan with a duct for floor sweep that evacuates the solvent contaminated air from the lower areas of each print station to keep the press room odor free.
Although there are screen interfaces on each unit, the Cerruti Press Operator system is the cardinal control interface based on a personal computer installed in the main console. It relies on graphic representations of the presetting cycle; diagnostics with a display of faults and press finish causes with electrical cabinet reference indications. Each error and press stop is recorded in memory. The system graphically displays the press layout with operating conditions and as a matter of course gives real time feedback on printing speeds, partial and full production footage as well the historical trends of air temperatures and speed. The Pelican Cerutti R982 shown in Gandhinagar is still in the factory along with a 2d press that is built undergoing daily tests and demonstrations. Although sold, Shah is committed to having the press perfect before shipping information technology to the customer.
Pelican presses and equipment tend to be strongly built, over-engineered perhaps, as Shah admitted to us, "There are reasons for this that emanate from my extensive knowledge of how these machines are actually run twenty-four hour period in and twenty-four hours out with various laminates on the shop floor." Although Pelican is a summit-notch engineering science business firm with Shah as the master designer, the company has become a mod engineering science firm. "Our next generation design professionals are relying on the software for both component and car design where component and press enhancements can be nigh tested for a variety of conditions without wasting materials or time," he adds.
Although parts of the electric current Pelican manufactory are brand new, the company has outgrown the facility as it works on several other equipment ideas. Information technology needs to increment its manufacturing capacity from 18 gravure presses a year to 24. Another new plant in Rajkot is set with its showtime 100,000 square of what will eventually be a 300,000 square pes facility. The entire assembly of the Pelican's gravure presses will be shifted there in the next few weeks.
Source: https://packagingsouthasia.com/packaging-production/first-cerruti-pelican-r982-press-ready-to-ship-to-customer/
0 Response to "First Cerruti Pelican R982 press ready to ship to customer"
Post a Comment